
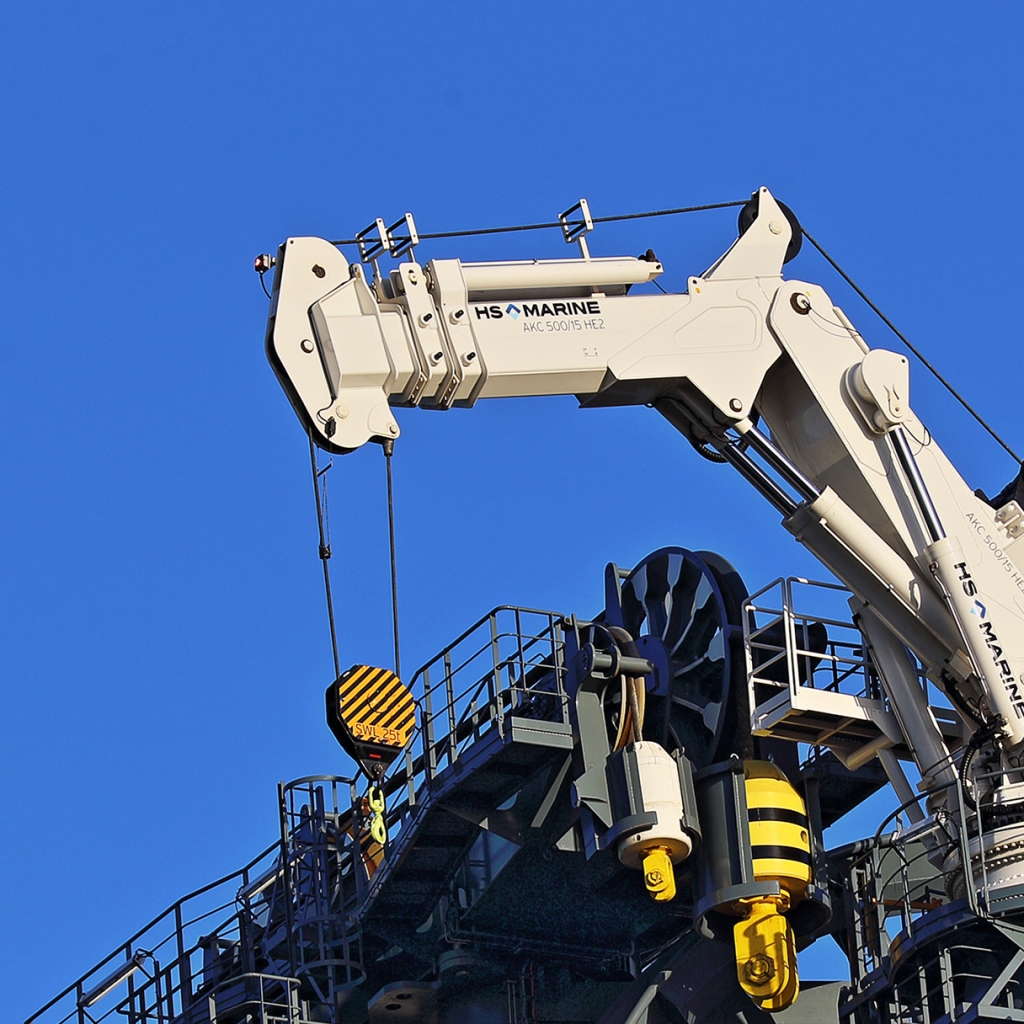
Special relationships for solids injectors and separators are developed. The relationships include the basic slurry flow equations for a pipe network and an additional set of equations for continuity of the solid phase. This report develops the relationships needed to analyze steady flow of a solid-liquid slurry in a network of pipes.
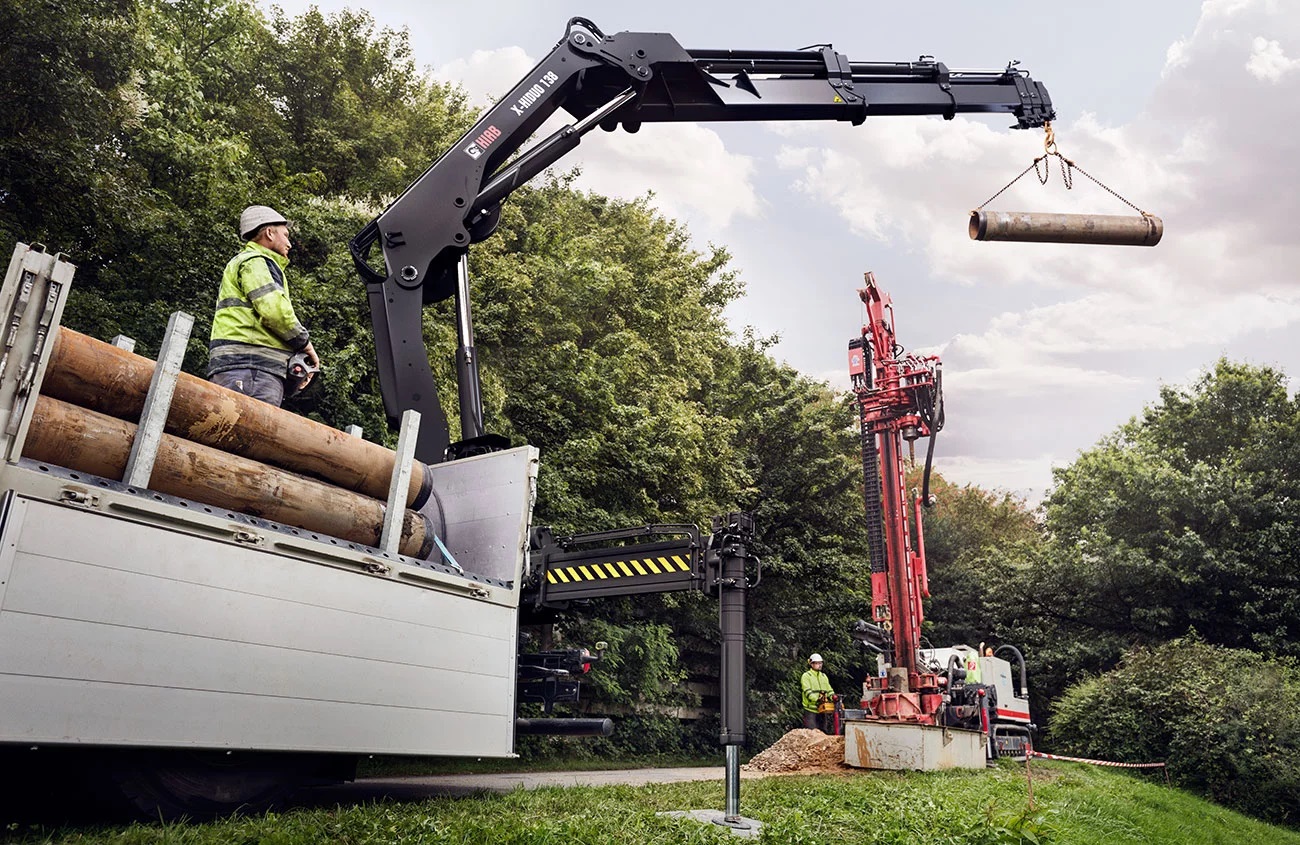
Laboratory and field testing are required to determine applications. Advantages and disadvantages of each method are assessed qualitatively. Methods assessed include pulsed air injection, vibration augmentation, friction reducing surfactant injection, and mechanical or hydraulic boring machinery. A limited qualitative analysis of methods proposed to unplug large particle pipelines is presented. Additional data from a systematic experimental program in a once-through pipeline system are necessary to further verify the modeling approach. Most available data, however, are neither extensive enough nor accurate enough to form complete conclusions as to the minimum operating conditions predicted with the force balance modeling approach. Results show agreement with some data sets and disagreement with others. Comparisons with data are made where possible and a step-by-step solution procedure is presented. Numerous flow phenomena and parameter dependencies are included in analysis of predictions made using the force balance modeling approach. They included measurements of the particle size dependence and flow geometry dependence on interfacial friction factors, initiation of plug flow motion, and more » plugging tendencies of flow through upward-turning elbows. These tests were designed to investigate isolated flow phenomena related to lower limits of operation of large-particle transport.
Crane pipe data series#
Results of four series of tests in a 35 m-long, 0.165 m-diameter plexiglass pipeline are presented. These phenomena are related to the mechanistic force balance modeling approach to predicting nominal and minimum horizontal pipeline transport conditions. These include particle suspension mechanisms, relative in situ slip between phases, and shear between separated solid/liquid flow regions. Large-particle hydrotransport flow phenomena are analyzed. In the ‘Rennels’ method, rc is limited to 0.5 or above which representsĪ sharp, square, inner edge - and an outer bend radius of 1.0.= , This as a multiplier of nominal diameter, which is different than actualĭiameter. When inputting bend diameters, note that manufacturers often specify One of ‘Rennels’, ‘Miller’, ‘Crane’, ‘Crane standard’, ‘Ito’, or Specified) used only in Miller method, method str, optional Or flow disturbances downstream (assumed 20 diameters if not The length of unimpeded pipe without any fittings, instrumentation, Rennels method if no friction factor given), L_unimpeded float, optional Roughness of bend wall (used in Miller, Ito methods primarily, and Rennels method if no friction factor given), roughness float, optional Reynolds number of the pipe (used in Miller, Ito methods primarily, and Number of diameters of pipe making up the bend radius Re float, optional Radius of curvature of the entrance, optional bend_diameters float, optional (used if rc not provided) Provided from Reynolds number, diameter, and roughness rc float, optional \Īngle of bend, fd float, optionalĭarcy friction factor used only in Rennels method calculated if not Flow of Fluids Through Valves, Fittings, and Pipe. National technical information Service, 1966. Soprotivleniyam, Koeffitsienty Mestnykh Soprotivlenii i Soprotivleniya Local Resistance and of Friction (Spravochnik Po Gidravlicheskim Handbook of Hydraulic Resistance: Coefficients of Internal Flow Systems: Design and Performance Pipe Flow: A PracticalĪnd Comprehensive Guide. ‘Miller’ returns 0.5093, and ‘Rennels’ returns 0.57. ‘Idelchik’, ‘Crane’, or ‘Miller, Returns K floatĠ.5 is the result for ‘Swamee’, ‘Blevins’, ‘Idelchik’, and ‘Crane’ The method to use one of ‘Rennels’, ‘Swamee’, ‘Blevins’, ‘Miller’ method recommending ~0.51 as read from a graph. The most recent ‘Rennels’, method recommending K = 0.57, and the Six sources are available four of them recommending K = 0.5, Returns loss coefficient for a sharp entrance to a pipe.
